When you're deciding between horizontal directional drilling (HDD) and vertical drilling, consider the project's scale and environmental footprint. HDD, with its ability to navigate under obstacles, offers minimal surface disturbance, making it ideal for congested urban environments or sensitive ecological areas. Conversely, vertical drilling provides a direct route to deep-seated resources, essential in oil and gas extraction. Each method has its merits, but the choice hinges on specific site conditions and goals. What factors might sway your decision toward one technique over another?
Understanding Horizontal Directional Drilling
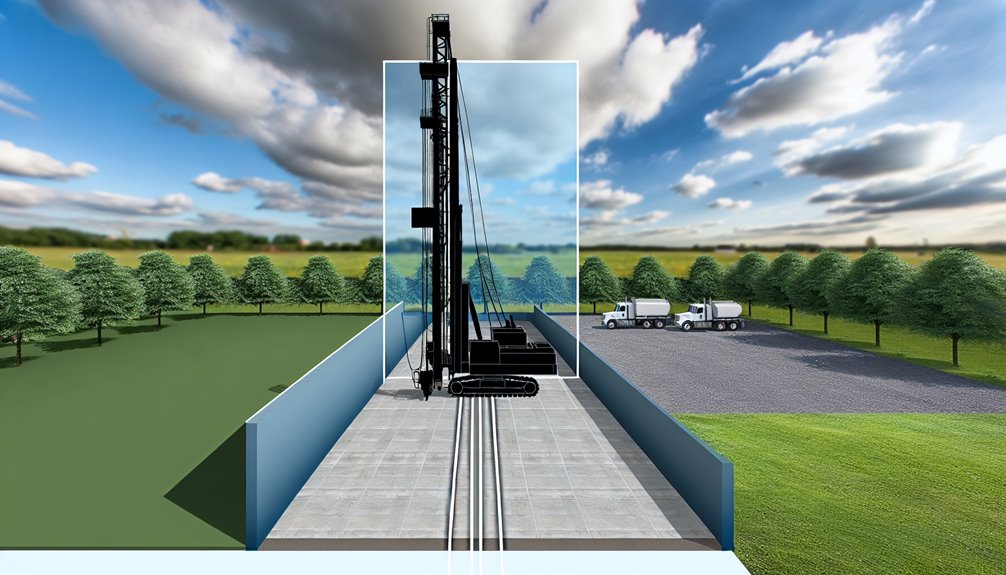
While horizontal directional drilling (HDD) may seem complex, understanding its basic process can considerably enhance your grasp of its applications and benefits.
Key to HDD's efficiency are the advanced drilling techniques and meticulous equipment selection tailored to specific project needs. Initially, you'll use a directional drilling machine to create a pilot hole, employing drilling fluid to navigate and extract soils. Precision in this stage is essential, as it determines the trajectory and success of subsequent operations.
Optimal equipment selection, particularly regarding the drilling machine and tracking system, directly impacts the accuracy and efficiency of the bore path. During the pilot hole phase, a transmitter near the drill head sends signals to the location engineer, providing critical data on depth, alignment, and slope, which are vital for accurate directional adjustments.
Your choice in HDD equipment must align with the soil conditions and the project's scale to guarantee minimal disruption and maximal effectiveness.
The Fundamentals of Vertical Drilling
You'll find that vertical drilling techniques hinge primarily on the deployment of conventional rigs to create a straight, downward path to access subsurface hydrocarbon layers. These methods serve critical roles not only in initial explorations but also in detailed reservoir characterization, making them indispensable in both offshore and onshore operations. Vertical wells are particularly efficient in offshore settings where the complexity and cost of directional drilling are significantly higher, reflecting their ongoing relevance in the industry offshore oil extraction.
Vertical Drilling Techniques
Understanding the principles of vertical drilling is essential when exploring the various techniques used in this method.
You'll begin with spudding techniques, where a spud bit creates a shallow initial hole, ensuring stability for deeper operations.
Then, you'll likely employ rotary drilling, a predominant technique characterized by a rotating drill bit connected to a drill pipe. This method is highly effective across diverse geological formations, providing you precise control and efficient penetration.
Rotary drilling's success hinges on its integration with other critical components like mud circulation systems.
These systems cool and lubricate the drill bit, stabilize the wellbore, and facilitate the removal of cuttings, ensuring continuous operation and minimizing potential downhole problems.
This streamlined process underscores the technical sophistication inherent in modern vertical drilling operations.
Vertical Drilling Applications
As you explore the domain of vertical drilling, it's important to understand its diverse applications, which range from well workover operations to geothermal energy production.
In well workover, vertical drilling is essential for accessing and isolating problem zones within wells, greatly enhancing well intervention measures and extending the operational life of mature wells. This method is integral in both secondary recovery, like waterflooding, and tertiary techniques such as enhanced oil recovery, improving drilling efficiency by mobilizing hard-to-reach oil reserves.
Additionally, in geothermal energy production, vertical drilling is key for tapping into deep underground hot water reservoirs, offering a reliable and straightforward approach.
This drilling method not only maximizes resource extraction but also minimizes environmental impact, aligning with innovative, sustainable energy solutions.
Technological Requirements for HDD and Vertical Drilling
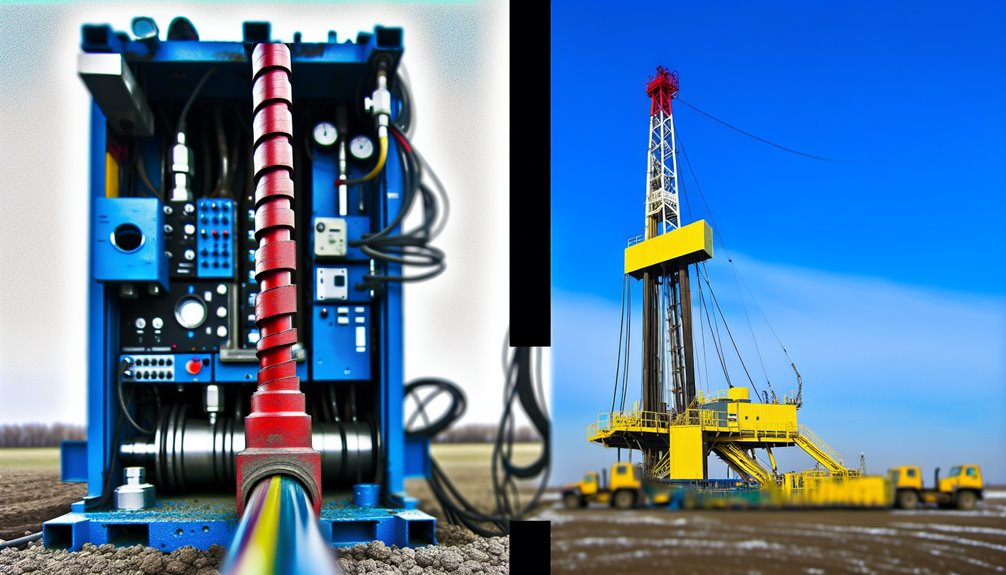
To effectively undertake horizontal directional drilling (HDD) or vertical drilling, distinct technological setups are required. Each approach influences your project's drilling efficiency and timeline.
Here's a precise breakdown:
- Drilling Rig and Equipment: HDD utilizes an inclined ramp with a complex hydraulic system for variable angle operations, essential for the project's flexibility. In contrast, vertical drilling employs a simpler vertical mast suitable for direct downhole progression.
- Drilling Fluids and Mud Systems: HDD demands advanced fluid systems with recycling capabilities to manage the horizontal drilling dynamics, whereas vertical drilling uses more straightforward mud systems.
- Guidance and Survey Systems: HDD requires sophisticated guidance and survey systems to navigate under various obstacles, markedly differing from the minimal guidance needed in vertical drilling.
Environmental Impact Comparison
As you compare the environmental impacts of horizontal versus vertical drilling, it's essential to assess how each method affects ecosystem disturbance levels.
Horizontal drilling often results in less surface disruption, which is a significant advantage over vertical drilling that typically requires larger and more numerous surface sites.
However, you must also consider the contamination risks, as horizontal drilling can pose challenges in managing inadvertent returns of drilling mud and fluids, potentially affecting nearby water bodies.
Ecosystem Disturbance Levels
While comparing horizontal and vertical drilling, it becomes clear that horizontal drilling techniques greatly minimize ecosystem disturbances. This method aligns with your innovative drive, focusing on ecosystem preservation and disturbance mitigation efficiently.
- Surface Disruption Minimization: It preserves green spaces by enabling underground installations without visible surface disturbances, effectively reducing habitat destruction and soil erosion.
- Impact on Sensitive Areas: Horizontal drilling bypasses sensitive areas like wildlife habitats and waterways, minimizing environmental impact and preserving natural landscapes.
- Habitat and Wildlife Protection: It reduces noise and habitat disruption, protecting biodiversity and supporting the preservation of aquatic and terrestrial wildlife.
Contamination Risks Analysis
Having established that horizontal drilling techniques can effectively minimize ecosystem disturbances, it's important to contemplate the environmental risks associated with these methods, particularly regarding contamination risks to groundwater and surface water.
HDD interconnects aquifers of differing qualities, potentially introducing contaminants from impacted geologic units into pristine aquifers. Drilling mud and fluids, particularly during inadvertent returns, pose significant threats as they can leak into both groundwater and surface water, increasing turbidity and altering water chemistry.
Such contamination sources not only disrupt aquatic life but can also degrade water supplies essential for agriculture and drinking. Implementing routine water quality monitoring and stringent protective measures is vital to mitigate these ecological consequences and safeguard environmental health.
Cost Analysis: HDD vs. Vertical Drilling
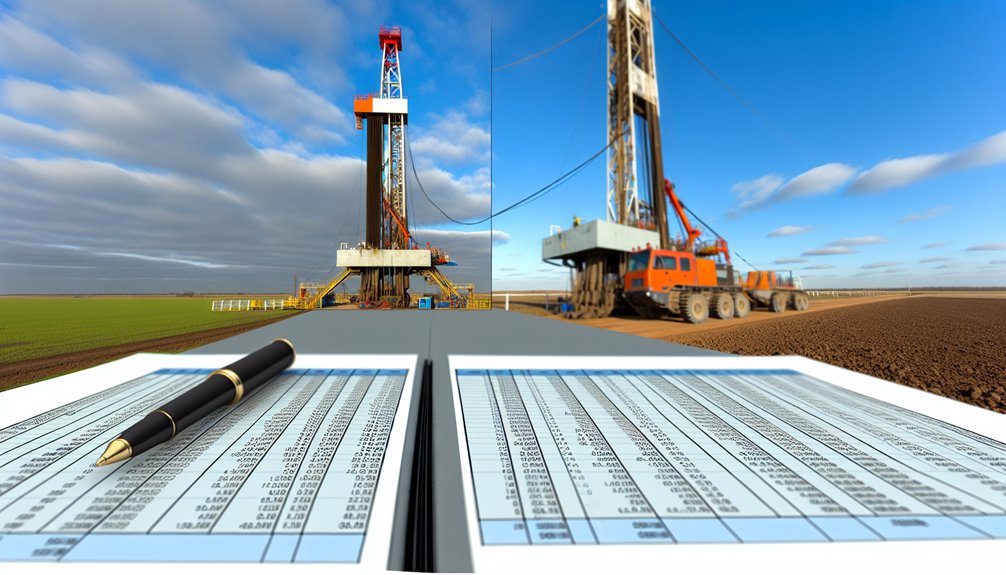
When comparing the costs of horizontal directional drilling (HDD) and vertical drilling, it's vital to evaluate both per foot expenses and total project costs. Understanding these cost factors is important for effective project budgeting.
- Per Foot Costs: HDD varies from $10 to $30, influenced by location and soil conditions. Vertical drilling doesn't typically offer per foot pricing, focusing instead on extensive project fees.
- Labor and Equipment Expenditures: HDD labor costs range from $35 to $45 per hour. Equipment choices, such as drill rigs and survey tools, also impact the overall budget.
- Environmental and Restoration Savings: HDD often incurs lower restoration costs, potentially reducing expenses by up to 46% compared to open-cut methods, favoring budget-conscious projects.
Applications in Construction and Resource Extraction
As the construction and resource extraction industries evolve, the applications of horizontal directional drilling (HDD) and vertical drilling have become increasingly critical.
HDD's ability to install utilities with minimal surface disruption enhances construction safety and boosts drilling efficiency, particularly under urban landscapes or sensitive ecosystems. This method supports rapid infrastructure modernization without significant environmental or community impact.
In contrast, vertical drilling remains indispensable in oil and gas extraction, providing direct access to subterranean resources. It's pivotal for conducting geotechnical investigations that determine site feasibility, ensuring safety in subsequent construction phases.
Both techniques are instrumental, yet their applications hinge on precision and strategic planning to meet contemporary demands in resource extraction and infrastructure development.
Challenges Faced in Horizontal and Vertical Drilling
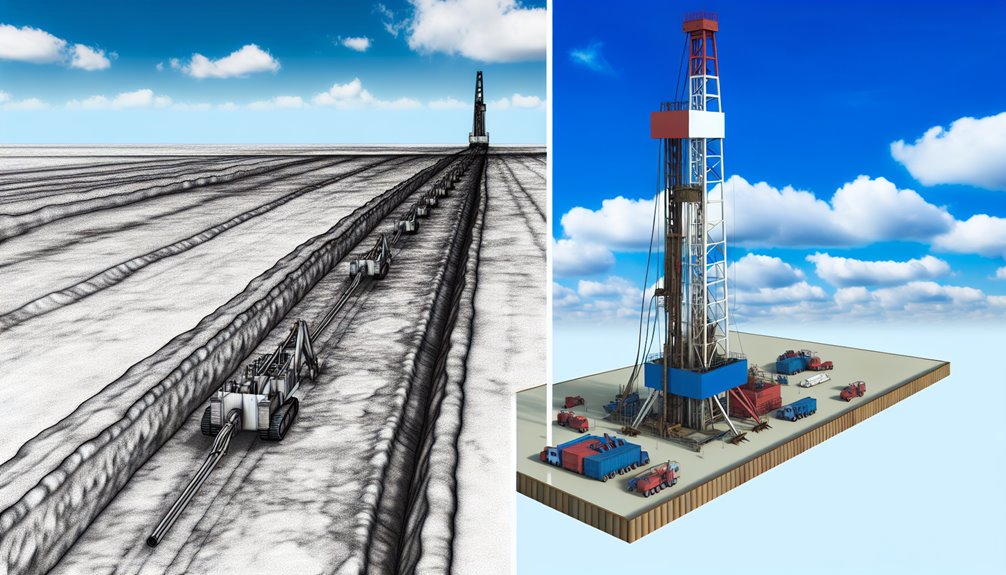
Despite the technological advances in drilling, both horizontal directional drilling (HDD) and vertical drilling present significant challenges that demand meticulous planning and precise execution.
You'll need to navigate complexities in project management and the selection of drilling techniques.
Here are key challenges:
- Soil and Rock Conditions: Different terrains necessitate specialized drill bits and methods. Hard rock and clay soils, for instance, may increase the risk of borehole collapse or fluid loss.
- Existing Utilities and Obstacles: Accurate mapping and advanced detection technologies are critical to avoid damaging underground utilities and guarantee precise drilling.
- Drilling Fluid Management: Selecting appropriate fluid types and managing their properties efficiently is essential to minimize environmental impact and operational disruptions.
Advancements in Drilling Technologies
Steering the challenges inherent in both horizontal and vertical drilling, the industry has responded with significant advancements in drilling technologies. Sophisticated drill bits and state-of-the-art navigation systems now enhance precision, guaranteeing the integrity of underground utilities and natural habitats.
This technology integration allows for real-time adjustments, minimizing environmental impacts and bolstering safety.
Automation in horizontal directional drilling (HDD) reduces the need for on-site personnel, increasing safety in hazardous conditions. Automated steering systems, utilizing real-time data and advanced algorithms, guarantee precise control.
Remote monitoring capabilities enable proactive maintenance and timely troubleshooting, enhancing operational consistency and productivity.
Furthermore, advancements in drilling fluids and mud recycling systems emphasize environmental responsibility while maintaining effectiveness, reducing both impact and operational costs.
Choosing the Right Drilling Method for Your Project
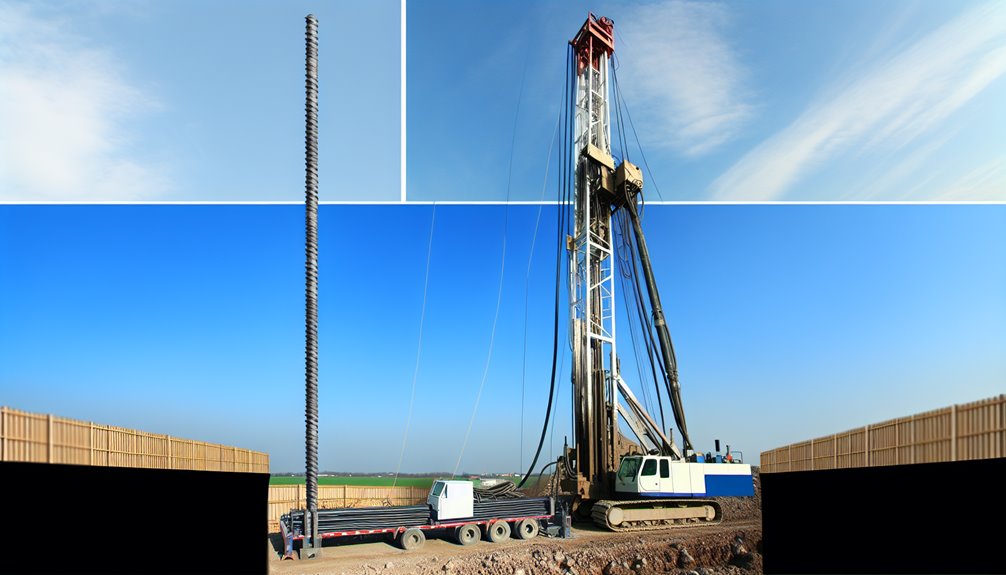
Why choose one drilling method over another for your project? Your drilling method selection hinges on a thorough project requirements analysis, ensuring alignment with your operational objectives and ground realities.
Here's what to take into account:
- Geological Analysis: Evaluate rock formations and soil types to determine the suitable drilling technique and equipment capabilities.
- Project Scope and Budget: Align your drilling method with the project's depth, diameter, and financial constraints.
- Environmental and Safety Compliance: Choose a method that adheres to environmental regulations and enhances safety at the drill site.
Conclusion
As you assess your project's needs, weigh the advantages of HDD's minimal surface impact against Vertical Drilling's depth access. Consider HDD for urban and cross-country applications where disruption must be minimal, and opt for Vertical Drilling when tapping deeper geological formations. Analyze cost-effectiveness based on the specific scope and environmental regulations. Your choice should strategically align with project demands, technological availability, and environmental stewardship, ensuring ideal efficiency and compliance.
If you're curious to learn more about the best drilling methods for your project, I invite you to visit Boring Bros at boringbro.com or give us a call at (954) 639-6167. We're here to help you find the perfect solution for your needs in a friendly and approachable way!